If you're weighing the pros and cons of hardwood flooring for your next home improvement project, there are several factors to consider. Solid hardwood floors, while beautiful and classic, usually require a hefty upfront investment. Cash-strapped homeowners might consider other materials, like engineered wood, which is made of composite materials that incorporate some real hardwood, or laminate flooring, a synthetic wood imitation that's typically easy to install, relatively cheap and durable.
Hardwood flooring is a natural product cut from a single piece of wood that's usually three-quarters of an inch thick. Engineered wood refers to a layered product with a thin slice of hardwood atop a composite core, like cork or plywood. Laminate is also a multilayered product, of mostly synthetic materials, with a high-resolution image of wood on the top layer. Engineered and laminate flooring are typically much thinner than solid hardwood.
Video of the Day
Video of the Day
The benefits and downfalls of wood versus laminate are multifold: Each material varies in price, look and durability, and performs differently depending on its environment, grade level, subfloor and underlayment.
Real Hardwood Flooring
Authentic wood floors aren't cheap or easy to install, but their presence can boost a home's resale value for decades to come. That's because this type of flooring is a great candidate for refinishing: It typically starts out at three quarters of an inch thick — more than double the thickness of the real wood layer of engineered hardwood — and can be sanded down and stained every 15 years or so.
On the lower end, the most cost-effective materials (cherry, hickory) run $2 to $8 per square foot, while those on the higher end, like ash and mahogany, can top out at $14 to $18 a square foot. Factor in professional installation and those numbers are closer to $12 to $23 per square foot.
"There's an initial outlay of capital for hardwood but you can refinish it until you get down to the tongue and groove," says Josh Veselsky, co-owner of the Chicago-based millwork and general contracting company Vero Design + Build.
Solid wood flooring is installed in a manner that leaves a gap between the floor and the wall, which is typically hidden by molding. This allows it to expand and contract as your home's humidity fluctuates. For this reason, hardwood is not ideal for high humidity areas like bathrooms, or basements, where concrete is the only subfloor. Hardwood does best when installed over plywood, plank or oriented strand board (OSB) subfloor.
One of the biggest draws of hardwood is its ability to change with each new owner's taste over the course of a home's lifetime and still last 60 to 100 years. "As a contractor, I almost never see a hardwood being removed — as long as it's being maintained — whereas the laminate and engineered wood have issues over time," says Veselsky.
Site-Finished vs. Pre-Finished Hardwood
Within the hardwood category, there are two types: site-finished and pre-finished hardwood. "Site-finished" refers to conventional unfinished wood planks that are installed and then, as a completed floor, stained and covered with a protective layer. "Pre-finished" refers to planks that are stained and finished in a factory ahead of installation. Pre-finished wood floors are a godsend for the time-starved because the job site doesn't have to be cleared to finish the floors, and if a section gets damaged, it's easier to remove individual pieces and reinstall them than redoing a whole swath of surface.
Veselsky warns to watch out for cupping, or swelling, with pre-finished wood flooring. The way pre-finished boards "click" together at installation can leave small gaps between the planks, creating an opportunity for moisture, dirt and debris to seep in.
Engineered Wood Flooring
Somewhere between solid wood and laminate, engineered wood provides a hardwood look that's easier to install, handles moisture better and can still help your home's resale value. "It's typically made of a synthetic core like cork or plywood for sound control, with an actual hardwood veneer that can be up to a quarter-inch thick," Veselsky explains.
This core is usually made from recycled materials, and the top layer is often sustainably harvested, making engineered wood an environmentally friendly option. Look for the FSC logo, which means the wood product has been ethically sourced and certified by the Forestry Steward Council. This is especially important for exotic species like ipe (pronounced "ee-pay"), also called Brazilian walnut, and mahogany.
The cost of engineered wood floors average between $3 and $5 per square foot for the material itself, plus another $3 to $10 per square foot for installation. And because it holds up against moisture better than the real thing, it can be installed in half-baths and basements when an appropriate subfloor is in place. Basements with radiant heat and multi-family residential buildings with concrete subfloors are common locations for engineered wood.
Downsides of Engineered Wood Flooring
On the downside, engineered wood flooring doesn't last as long as solid hardwood and can only be refinished once or twice before the veneer starts to wear away. The selection of wood is limited in the engineered category as well: You won't find soft woods like pine and Douglas fir in engineered form.
Veselsky says homeowners need to do their due diligence before installing engineered floors. "Have a home environmental company conduct a moisture test beforehand," he says. If you're working with new construction — where concrete was poured in the last 30 days or plumbing was recently fixed — there's still moisture in the atmosphere that could cause cupping or separation of joints in the wood.
Where engineered wood is stored during assembly and before shipping can affect how it contracts or expands. Engineered product should sit on the job site long enough to become homogenous with its environment so that when it's eventually laid down it performs as it's supposed to, according to Veselsky.
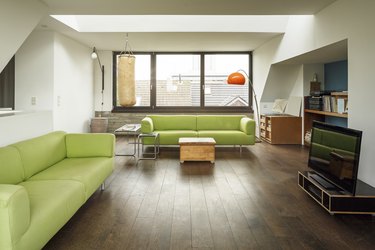
Laminate Flooring
This layered synthetic product consists of a high-density fiberboard sandwiched between a thin decorative layer that mimics the look of real wood and a backing board for stabilization. It's usually 3/8 to 5/8 of an inch thick, much thinner than hardwood.
At $3 to $8 per square foot, including materials and installation, laminate floors are the most economical option and, as such, won't do much for your home's resale value. "Laminate is commonly used in a commercial setting," says Veselsky. "It's good for a tenant who's on 10-year lease. In a residential setting, we like to pretend we're going to live somewhere for 15 years or more."
Buyers need to be deliberate about their laminate aesthetic because it can't be customized or refinished after the fact. A trendy look today can create waste later on. "If you don't like a dark stain that's in place with hardwood, you can sand it and leave it natural or stain it to your liking," says Veselsky. "Even engineered wood can be refinished a couple of times. Laminate is a picture of real wood, so if the next homeowner gets stuck with something they don't like, they're going to rip it up."
The durability of laminate is one of its biggest benefits: It can resist scratches, stains and mold, and even have antimicrobial properties, so it's a good option for families with children and pets. On the flip side, one of its biggest drawbacks is that if a section is damaged, the whole floor may need to be replaced to maintain a consistent look throughout.
Installing Laminate Flooring
Laminate is easy for DIYers to install and, as a type of "floating flooring," can be placed, along with an appropriate underlayment, on top of many existing floors. You'll want to be mindful of repeating wood grain patterns on the planks if you go this route. Because laminate is completely man made, there are a set number patterns, and placing two identical boards next to each other will be a dead giveaway they're not the real deal. It's also important to install laminate on a completely level subfloor — its thin nature means it's unforgiving to lumps and bumps underneath.
Laminate flooring can warp when it comes in contact with moisture, so it shouldn't be installed in wet environments like bathrooms, kitchens or laundry rooms. Likewise, it shouldn't be cleaned with steam or wet mops — according to Shaw Floors, floor manufacturers recommend sweeping or vacuuming regularly, and spot cleaning as needed with a damp cloth.
Can You Waterproof Wood Floors?
There's no responsible way to make a wood floor waterproof or even highly water resistant, says Veselsky. "Your hardwood floor was a living, breathing tree, likely less than a year ago if it's new," he adds. "It's not a best practice to encapsulate it with an epoxy — that hinders wood's ability to breathe and expand and contract in summer and winter."
It's possible to waterproof the substrate or surface below the floor, but that isn't ideal either: If water spills on the floor and can't go below, it will spread to floors in neighboring rooms. In this scenario, waterproofing does more harm that good — you're better off replacing ceiling drywall in the basement or apartment below than large sections of hardwood. Similarly, water that migrates through the seams between the boards and gets trapped underneath or can't evaporate because of "waterproofing" can lead to mold issues.
Certain species of hardwood are, however, more water resistant than others. "Old homes used maple because you very rarely have cupping with it, unless you have a slow drip. A spill evaporates," Veselsky explains.
The term "waterproof laminate" is used to describe engineered vinyl plank (EVP) flooring, which is somewhat more water resistant than standard laminate. EVP is tile with a fiberboard core and is often used in kitchens and baths because doesn't take on water, aside from where the baseboard meets the seams.
Before making a final decision and purchase, "have an experienced floor contractor advise you in addition to an architect and designer," says Veselsky. "Your contractor can tell you — for example, if your designer specifies a material like laminate — what experience they've had with a material, and offer a better spec on similar flooring that meets the look you're going for."