Wood is one of the most sought-after flooring materials among home buyers and remodelers. A survey of over 4,000 home buyers conducted by the National Association of Home Builders listed wood flooring as one of the top ten features desired in a new home. And it has been that way for a long time. Wood flooring is so popular that manufacturers of other flooring materials, such as luxury vinyl plank flooring, porcelain tile and laminate flooring, all produce products that mimic the look of real wood.
Wood flooring as a lot going for it:
Video of the Day
Video of the Day
- It's a classic building product that goes with any house style.
- It's a natural product that comes from a renewable resource.
- It's milled from a number of wood species, including bamboo and exotic imported woods, that all provide distinctive looks.
- It's available in a number of different colors and textures, thanks to modern finishing processes. These include matte and glossy finishes, as well as distressed and hand-scraped looks.
- Solid wood flooring can be sanded and refinished, prolonging the life of the floor.
- Thanks to the development of engineered wood flooring, there's a wood flooring product that can be installed anywhere in the home, including basements.
- Solid wood flooring can be recycled.
- It's available in a number of price points.
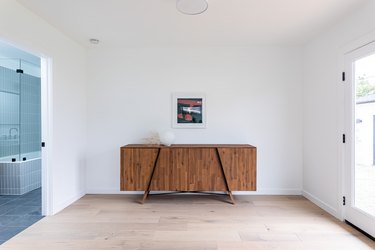
There are two types of wood flooring: solid and engineered.
Solid Wood Flooring
Solid wood flooring has been used in homes since Colonial times, and it is the product that most people envision when they talk about wood flooring. It's available in wood species grown in the U.S., such as white oak, red oak, hickory, maple and pine, but you can also find exotic woods, such as tigerwood or Brazilian teak.
Solid wood flooring is 5/8 to 3/4 inch thick; and it comes in widths that start at 2 1/4 inches, called strip flooring, and can go up to 7 inches wide and more, called plank flooring. Expect to pay about $3 to $14 per square foot. That includes everything from pine at the low end to an exotic species such as Brazilian walnut at the high end. Professional installation will cost another $3 to $10 per square foot.
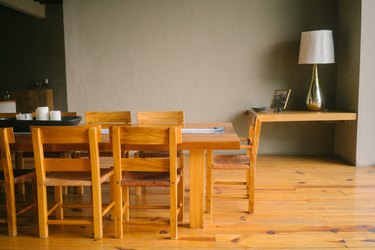
One of the advantages of wood flooring is that it can be installed in most rooms. Many people shy away from using it in kitchens and bathrooms because of possible water damage, but modern finishing techniques now make hardwood flooring more suitable for moist locations that was once the case. Make sure to check the manufacturer's recommendations for usage, as there may be restrictions that can affect warranty claims. Hardwood flooring may not be the best choice for family bathrooms prone to water spillage, but but it is not unusual to see wood floors in kitchens. Because of how it can react to humidity and moisture, solid wood should not be installed below grade or directly over concrete.
Purchasing Wood Flooring
Wood floors are sold through home centers, large flooring retailers, online sources and independent flooring stores. Generally, you are expected to pick the flooring you want based on a sample that is small enough to hold in your hand or, in the case of online retailers, on a small photo of the product. However, some larger retailers allow you to upload a photo of the room where you want the flooring to go, and then the application shows how different products will look in the room. That's helpful, but there are a few other things to consider when making a purchase.
The source: Most wood flooring manufacturers obtain the wood from managed tree farms. But if you are unsure of the source, check for the Forest Stewardship Council (FSC) seal. FSC is an international program that certifies wood products that come from sustainable and environmentally friendly sources. The program covers everything from proper forest management to fair labor issues.
Finished or unfinished: You have a choice, but factory finished products are becoming much more popular than site-applied finishes. With a prefinished floor you can start to use the floor as soon as it is installed. Once installed, an unfinished floor must be sanded, perhaps stained and then finished with a protective sealer. Prefinished is easier, but many people swear by the quality of the finish a good flooring contractor can provide.
*The grade: *All wood is graded based on how it looks. It's important to remember that a wood's grade has nothing to do with strength or durability. But wood is a natural product and it is going to have some "imperfections," such as knots, wormholes and the like. A product with the least amount of imperfections will be graded "clear" or "select." Boards with more imperfections might be labeled No. 1 or No. 2. Many wood manufacturers associations have their own grading systems, and some retailers have proprietary grading systems. The important thing is to check the grade, which you can find in the product's literature, and ask the salesperson to explain it.
Installing Solid Wood Flooring
Before installation, the wood needs to sit in the room where it will be installed for a few days so that it can acclimate to the humidity of the room. During installation, the boards are attached to a plywood subfloor that must be clean and flat. Low areas must be filled with a leveling compound to provide an acceptable surface.
Solid wood floors generally feature a tongue-and groove-design. Individual planks interlock with adjoining planks and are also nailed or glued to the wood subfloor. Baseboard molding installed around the perimeter of the room hides the edges of the boards.
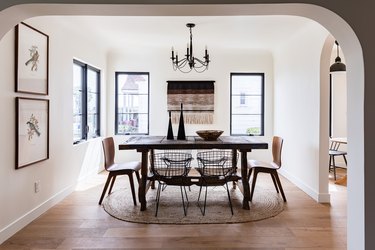
Reclaimed Wood Flooring
Lumber salvaged from buildings that were demolished is another source of solid wood flooring. In many cases, floors and walls of old buildings, including old barns, can be milled to produce distinctive looking flooring.
This type of material is not always easy to find. Architectural salvage operations are good places to start. If they don't have what you are looking for in stock, they may be able to source material for you.
Bamboo and Cork Flooring
Flooring made from bamboo and cork have both enjoyed some popularity in recent years, mainly because, like traditional hardwood, they are renewable resources. But the difference is that they renew much quicker than the typical tree species.
Bamboo, which is technically a grass rather than a wood, can regrow in five or six years — much faster than trees. Cork is actually harvested from the bark of the cork tree. The bark grows back in a few years. Some cork flooring may even be made from the cork of recycled bottle stoppers.
Bamboo flooring: Depending on how the flooring is processed, bamboo floors can look like traditional solid wood flooring, or it can have a distinctive look that you can't find in wood products. The product can be used anywhere, although high-moisture areas should be avoided. Bamboo is available in planks that can be glued down, nailed or installed with a click and lock system.
*Cork flooring: *A certain "give" underfoot separates cork from other wood-like flooring. Because it is comfortable to walk on, it is often used in kitchens, although it can be installed anywhere. Most cork comes in 12- or 24-inch square tiles that click and lock in place, although panels are also available.
Engineered Wood Flooring
Unlike solid wood flooring, engineered wood is made up of from three to seven thin layers of lumber or MDF that are bonded together. The top layer is a veneer of a hardwood species, such as oak or maple. The construction saves lumber, and it also makes the panels more dimensionally stable than solid wood. That means the products can be installed in basements or on concrete.
The cost for engineered wood, $3 to $12 per square foot, will overlap the costs of solid wood, especially in the low and mid ranges. More plies and a thicker veneer layer usually means a higher cost. The finish on the veneer layer is important because the finish on a 1 mm layer cannot be sanded and refinished. Thicker layers can be sanded, but only a certain number of times.
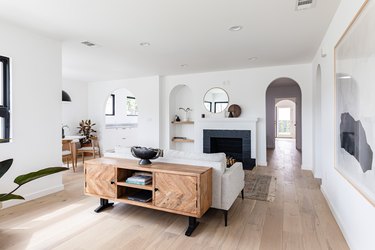
Purchasing Engineered Wood Flooring
All engineered wood flooring comes prefinished. There are a variety of colors and finishes available, including gloss, matte, distressed and hand scraped. As with solid wood flooring, the veneer layer is graded based on appearance.
Installing Engineered Wood Flooring
The flooring needs to acclimate to its surroundings before installation. Because of the design, engineered wood can be installed over wood, concrete and other hard surfaces. Usually a pad underlayment is required.
Some products must be glued down, other can be nailed and some have a click-in-place installation system whereby each panel is attached to the next, creating a floating floor. Baseboard molding hides the edges around the perimeter of the room.