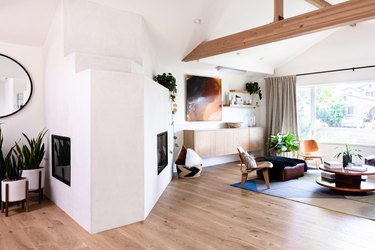
Although breathtakingly beautiful when they are well maintained, genuine hardwood floors are expensive to install and require vigilance when it comes to cleaning up spills. What about engineered hardwood? If you haven't considered this flooring option before, now is the time.
Engineered hardwood will give you the look and feel of real hardwood floors because it's made of genuine wood. It's manufactured differently than traditional wood flooring planks, however, to make it more dimensionally stable (less prone to expansion and contraction) and somewhat more resistant to moisture. Before you change your whole renovation plan, though, be aware that engineered wood floors do have a few drawbacks to consider.
Video of the Day
Video of the Day
Tip
Engineered hardwood is made by fusing together several thin layers of wood for strength and support. The top layer of the flooring is a thin hardwood veneer cut from a single log or board to showcase the wood grain and mimic the look of solid hardwood.
How It's Made
When you purchase a solid hardwood floor, it's made just as you would expect it to be. Lumberjacks fell trees and send the logs to the factory where they get cut into the planks that will make up the floor. After being cut and given a good sanding, a machine cuts tongues and grooves into the planks so they fit together tightly when installed. The completed planks are then prefinished or shipped to the customer unfinished so you can apply the stain and sealant of your choice.
Like solid hardwood flooring, engineered wood is made from real wood. Each plank is not, however, milled from a single piece of wood. Instead, thin sheets of wood are glued together like layers of plywood. To add strength, the manufacturer positions each layer so that the grain runs perpendicular to the previous layer. The very top layer of the floor, also known as the wear layer, is a thin covering of hardwood shaved from a log.
When superior water-resistance is required, manufacturers sometimes replace the wood base layers of engineered hardwood with a stone plastic composite (SPC) material. Made of limestone and plastic, SPC is often used in commercial flooring and is completely waterproof. The floor's top layer is still wood, however, so you get the same look and feel.
Commercial-Grade Options
If you have your heart set on a wood floor but know your family is hard on things — maybe you have pets, or just a rambunctious toddler — consider getting a commercial-grade floor. When an engineered hardwood floor's final destination is a commercial environment like a restaurant dining room, manufacturers will strengthen the floor by impregnating it with acrylic.
To infuse a floor with acrylic, manufacturers place engineered wood planks in a vacuum after they're constructed. This removes all of the sap and natural sugars from the wood, leaving behind a hollow, cork-like structure. Liquid acrylic is then forced into the openings where the sap was, making the wood stronger. The end result is an engineered wood floor that is up to 300 percent stronger and more durable than it would be otherwise.
You'll Have Similar Options
Because both solid wood floors and engineered wood are genuine wood products, you won't have to sacrifice the wood you want if you opt for engineered flooring. The wooden top layer of your floor is available in a wide array of options, allowing you to choose from genuine hickory, acacia, white oak, red oak, Brazilian cherry and other wood species just as you can with a solid hardwood floor. If, for instance, you choose an oak engineered floor, you can expect to get the same look you would get if you opted for an oak hardwood floor.
Other flooring options remain the same as well. Engineered floors come in plank widths of 3 to 7 inches, so you'll have no trouble finding wide-plank flooring if you wish. Like traditional hardwood, you'll still get to choose between a high-gloss or matte finish as well. Although it's a bit harder to track down, you can even purchase unfinished engineered flooring if you wish and finish the floor yourself once it's installed.
Pros of Engineered Wood
Engineered hardwood floors are gaining popularity, and it's easy to see why. Given their rigid, genuine wood construction, these floors are just as durable as their hardwood counterparts when properly maintained. Floors made of engineered hardwood don't expand and contract as much as solid hardwood, so they're less likely to gap, and you can install them on solid subfloors like concrete.
Given their superior moisture-resistance, engineered hardwood with an SPC core is an option for kitchens, bathrooms, laundry rooms and other moisture-prone areas where hardwoods typically aren't recommended. This includes installation over in-floor heating systems, which aren't compatible with all solid hardwood floors but will generally work fine with engineered wood.
Those looking for an environmentally friendly solution will also find engineered wood to be the better option. The trees used to produce hardwood floors can be and often are replaced by seedlings when they're harvested. Some tree species grow slowly, however, and it can take a long time to replace one lost to flooring. Because engineered wood uses a thin top layer of wood rather than a solid plank, it takes far less slow-growing hardwood to produce an engineered floor.
Cons of Engineered Wood
If your solid hardwood floor starts to wear or show its age, you always have the option of sanding it down and refinishing it. You may not have this option if you choose an engineered wood floor. Only the top layer of an engineered wood floor is mean to be visible. If this veneer is too thin, sanding it will reveal the much less attractive wood layers underneath the surface.
You may have the option of refinishing engineered wood up to five times, but it depends on the quality of the floor you choose. Generally, high-quality engineered floors have thicker top layers and are more likely to withstand a refinish.
This is really the biggest negative of engineered wood. When made well, engineered wood is durable and more resistant to moisture problems than hardwood. Quality varies greatly from one product to another, however, and makes a big difference in how your floor will perform. Make sure you shop around and go with a brand or flooring dealer you trust.
More Alike Than Different
Engineered hardwood floors do offer some benefits over traditional hardwood, but they're still made from wood. As such, they do share some of wood's limitations. Although engineered wood is more water-resistant, it's not waterproof unless you opt for SPC engineered wood, and even then the top wood layer can be damaged by water. You'll have a bit more time to clean up spills on an engineered wood floor, but standing water can still cause issues. With careful maintenance, you can get away with an engineered wood floor in a kitchen or bathroom but not in a basement that occasionally floods.
Keep in mind too that all wood is susceptible to scratches. It's important that you avoid sliding furniture and other heavy objects on both traditional and engineered wood floors. You'll also want to keep your dog's nails trimmed. This is particularly important if you choose a softer wood like pine.
Both floor types require the same care as well. You'll want to sweep away any dirt with a broom. You can then wipe it with a slightly dampened towel or mop. Do not wet-mop any wood floor.
The Cost of Engineered Flooring
One of the most commonly cited advantages of engineered floors over hardwood floors is cost. It is true that engineered floors can cost significantly less than solid hardwood, but this isn't always the case. The prices of both types of flooring vary greatly depending on the type of wood used and its quality. Floor Critics breaks down the cost as follows:
- Softer solid wood floors, such as those made of pine, typically cost between $3 and $6 per square foot. A basic engineered wood floor with three core layers and a 1/12-inch-thick veneer layer costs about the same.
- Native hardwoods, such as cherry and oak, cost around $5 to $10 per square foot, and so do mid-grade engineered floors with five core layers and a wood veneer between 1/12 and 1/6 of an inch thick.
- Exotic woods like Brazilian walnut or mahogany sell for $8 to $14 per square foot, and so do high-quality engineered hardwoods with seven core layers and a veneer that is 1/6 of an inch thick or thicker.
As long as you don't get them wet or expose them to high levels of humidity, hardwood floors boast incredible longevity and durability. If you want your engineered wood floor to last as long as its solid counterpart, you'll need to spring for a high-end floor. While the flooring itself may cost similar amounts, the installation is your chance to save.
According to ImproveNet, installing engineered hardwood costs half as much as installing solid hardwood flooring. Traditional hardwood flooring typically requires nailing through the boards, which can prove difficult on true hardwoods. Engineered hardwood floors, however, often use a floating installation method that makes the job much quicker and easier. Engineered flooring is much easier to install as a DIY project as well, letting you skip the cost of a professional installer altogether if you're confident in your home improvement skills.
Choosing Healthy Flooring
When building or remodeling a house, it's naturally important to develop a budget for your project and try to stick to it. When it comes to engineered hardwood floors, however, bargain shopping can negatively impact your health. One way manufacturers can cut costs when building engineered hardwood floors is by using cheaper glue to hold the layers of the floor together. These glues don't hold as well and may allow the layers of your floor to separate over time.
Far more insidious, however, is the potential for these glues to leak formaldehyde into your home. As of 2018, the Formaldehyde Standards for Composite Wood Products Act protects U.S. consumers from dangerous levels of formaldehyde by holding manufacturers to strict production standards. Floors made prior to that, however, could contain higher than acceptable levels of formaldehyde, so be careful when floor sellers liquidate old inventory.
To stay on the safe side, look for floors that bear an NAF label, which means the product contains no added formaldehyde. Some floors also carry a California Air Resources Board rating. A rating of E1 or E0 under this system means the floor is safe.
Names You Can Trust
It's easy to advise that you buy a high-quality engineered hardwood, and lots of people will tell you to do so. When it comes to recommending a brand, however, most dealers will simply point you to whatever they happen to sell. You'll find shopping a lot easier when you know which product to seek, and one of the best is Somerset Hardwood Flooring. Somerset doesn't sell directly to consumers, so you'll have to look around for a dealer near you. Its amazing 50-year warranty makes the hunt worthwhile, however.
If you want to go green, take a look at what Tesoro Woods has to offer. This company sells zero-VOC products and makes its floors from reclaimed and recycled wood. If you want to finish your floors yourself, look into engineered hardwoods from Hurst Hardwoods. It's one of the few manufacturers that sells unfinished engineered hardwood floors, so you can finish your floor yourself and get exactly the look you want.
Of course, trusted favorites like Armstrong and Pergo also sell engineered wood floors and have excellent reputations. These well-known brands are easy to find no matter where you live and have a long history of customer satisfaction as well as a reputation for offering lots of affordable options.
Engineered Wood vs. Vinyl Plank
People often compare hardwood and engineered flooring to each other, but there is another contender worth mentioning. Vinyl plank flooring is made from several layers of PVC with a wood grain pattern printed on top. Unlike hardwood and engineered wood flooring, vinyl plank flooring is completely man-made.
Vinyl plank floors cost less than high-end engineered hardwood, with Floor Critics reporting the average price in 2018 between $1 and $4 per square foot. Installation adds another $7 per square foot to vinyl plank flooring costs. Although it looks like wood, vinyl plank is much more water resistant, and you can clean it with a wet mop. It also resists scratches better than wood floors.
Easy to install yourself and cost effective, vinyl plank may prove easier on your flooring budget. Note, however, that vinyl plank flooring lasts only five to 20 years, while engineered hardwood lasts between 20 and 100 years depending on the quality of the floor and the care it receives. It's also of note that although the pattern on vinyl plank can mimic wood grain, it will never be as random as what Mother Nature produces.

Installing Engineered Hardwood
Before you begin installing your engineered hardwood floor, make sure your subfloor is flat and in good shape. You'll then want to install a moisture barrier on the subfloor to protect the wood. When it's time to lay the wood planks, start in a corner and run your first row of boards along the longest exterior wall in the room. Hardwood Bargains recommends using 1/2-inch spacers between the first row of wood and the wall to allow for a bit of expansion.
Toenail the first row into place and then continue laying the floor a row at a time, snapping the tongues into the grooves in the boards as you go. Remember to stagger the ends of each board by about 12 inches so you don't end up with a row of seams. You can glue or nail the floor if desired, but a floating installation is easier and works fine for most applications.
When you're done laying the main floor, cut around door frames and any electrical outlets on the floor as needed. You can then install your baseboards or trim. When you're done, take a minute to admire your handiwork.
- BuildDirect: How is Hardwood Flooring Made?
- Floor Critics: Hardwood Flooring: Materials & Installation Cost
- ImproveNet: The Hardwood Flooring Dilemma: Laminate, Solid or Engineered
- Floor Critics: Vinyl Plank vs Engineered Hardwood Flooring
- Flooring Inc.: Engineered Hardwood vs. Laminate Flooring: What’s the Difference?
- Floor Critics: Hardwood vs Engineered Hardwood Flooring
- HomeAdvisor: Engineered Flooring: Easier Hardwood?
- Floor Critics: Engineered Hardwood Flooring: Reviews, Best Brands & Pros vs. Cons
- Hardwood Bargains: How To Install Engineered Hardwood Flooring