Beautiful pinks, rich greens, elegant blacks. Have you ever wondered where all those granite countertops in all those amazing and astoundingly different colors come from and how they get to your kitchen?
Granite is an igneous rock. That means it is volcanic in origin. Rather than flowing out of a volcano, granite forms underground when magma solidifies gradually without reaching the surface. Because it cools more slowly than erupted magma, it contains distinct and visible crystal patterns. Varied crystal sizes occur when the rock cools at different rates; faster cooling yields smaller crystal sizes.
Video of the Day
Video of the Day
The various colors of granite are due to the differing proportions of minerals contained in the stone. Potassium feldspar, sodium feldspar, and quartz are the primary components of granite and yield the gray, whitish-pink or salmon-pink granite commonly seen in buildings and monuments. Biotite adds black or brown tones; amphibole adds black or green; and muscovite adds yellow.
There is a difference between this geological definition of granite and the commercial definition. In the commercial sense, any hard stone or any stone that is not marble is often called granite. Because the definition of granite requires that it contain 20 percent quartz, which is usually white or clear, so-called black "granite" is likely a rock called gabbro. Other igneous rocks that are commonly sold as granite include diorite, andesite, syenite, anorthosite, basalt, and granulite. In the commercial industry, gneiss and schist are metamorphic rocks that are also sold as granite.
Note that quartz countertops are a manufactured product made of ground quartz bound together with resins.
Mining Begins at the Quarry
The manufacture of granite countertops begins with mining dimensional granite from quarries. Dimensional means that the rock is cut in whole pieces as opposed to quarried for crushed stone. In the United States, granite is mainly quarried in New England (New Hampshire is known as the Granite State), Texas, Indiana, Wisconsin, and Georgia, but there are granite quarries located in thirty-four states. However, most of this granite is used for building exteriors, floors, and grave markers, due to the predominance of grays, pinks, and whites. The more colorful granites are from elsewhere—predominantly India, Brazil, and Norway.
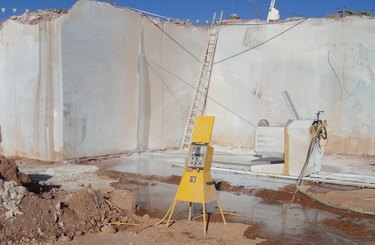
Granite is quarried in open pits. Because granite is fairly common, deposits that are not easily accessible are not typically quarried unless the color or pattern is unique. The first step is to remove the overburden—the soil or gravel laying on top of the granite. Undesirable sections of stone are removed by drilling and blasting. At one time, granite was quarried by blasting, but now diamond wire saws are more commonly used. Vertical and horizontal holes are drilled through the stone and a wire saw is threaded through the holes.
Stone Is Cut Into Blocks
The wire saw is a cable with regularly spaced diamond beads. Once threaded through the holes, the cable is spliced together and mounted on a large engine that drags the wire on a continuous loop through the stone while also backing up to maintain tension on the wire. These cuts with the wire saw will release a very large piece of stone—30 to 50 feet wide and tall by 6 to 9 feet deep. A soft bed of dirt is prepared and the large chunk is pushed off the rock face with wedges, airbags, excavators, or explosives. Sometimes the chunk shatters or fractures at this stage, which obviously is undesirable!
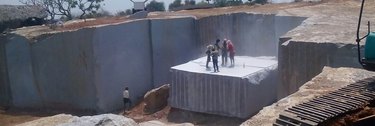
The large chunk is then divided into smaller rectangular blocks by drilling numerous vertical holes and inserting either explosives or expanding mortar. This produces the distinctive edges seen on raw granite slabs in the warehouse.
A Block Becomes Slabs
The large blocks of granite are then further cut down into slabs, usually at the quarry, by giant gang saws. A gang saw has dozens of equally spaced parallel blades or parallel wires. The blocks are loaded into the saw and the entire block is cut into multiple slabs simultaneouly—a process that may require 40 to 50 hours. (When cut with diamond wire cutters, the time is substantially less.) Slabs are either 3/4 or 1 1/4 inches thick (2 or 3 cm). The slabs are usually about 9 x 6 feet (3 x 2 meters) in size. The slabs are then polished on one side, bundled together with slabs from the same block, loaded into containers, and shipped out to distributors. The slabs are bundled together to ensure that buyers can acquire multiple slabs that are similarly colored and patterned.
The most common finish for granite is polished, but honed and leathered are finishes gaining more appeal. The non-polished finishes are applied at the fabricators. The polished finish reveals all the colors and patterns of the stone in high definition, but it also is very reflective and therefore reveals any smudge of dirt on the surface. Honing simply removes the high shine from the polished surface. The patterns in honed granite will be muted, and the surface is no longer reflective. Leathering is a textured surface created by blasting the surface with water jets to remove softer areas of stone, then brushing the surface to smooth rough edges.
A Slab Becomes a Countertop
The first step in converting huge slabs of stone into countertops is a design meeting with the consumer, architect or designer, and fabricator. The consumer may choose to go to the warehouse and choose a slab, or may leave that to the designer. Fabricators have sample squares on hand, but because granite is a natural product, many variations occur, even between slabs cut from the same block.
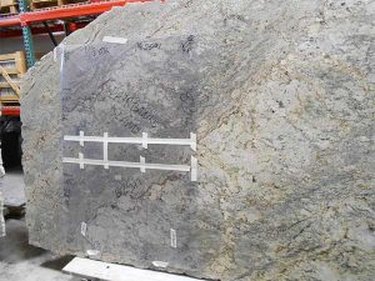
Fabrication begins after the cabinets are installed. Measurements are critical for a good outcome, so the area is either measured with a laser measuring system, or templates are made from plywood or foam core. The measurements are then fed into a computer design program, which lays out the cuts on a slab. Some shops use high-definition photos of the slab to lay out the cuts to maximize pattern matching, while others use clear plastic templates to pattern-match.
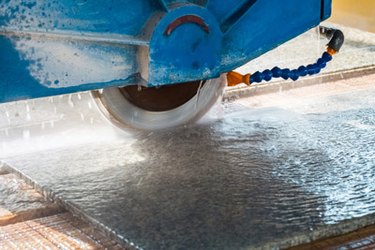
The slabs are cut to the dimensions for each project using a computer controlled diamond blade wet saw or water jet. Usually, about 20 to 30 percent of a slab is discarded due to weak points in the stone or the presence of unwanted patterns. The edge treatment, if not simply squared off, is shaped using a router. The edge treatment is then polished or honed to match the surface. Some fabricators cut sink and faucet holes in the shop, while others cut those holes on site using diamond blade saws.